Various Performance Tests That Maintain the Quality of Our Products
Paint Layer Test
system | tensil stregth N/mm2 |
tear resistance N/mm |
elongation % |
---|---|---|---|
A-1 | 0.70 | 7.20 | 200 |
B-1 | 1.36 | 9.60 | 45 |
Method
JIS A6021 paint waterproofing materials for architecture was applied.
The curing condition was 232
with 50
5% RH, and it took place for four weeks.
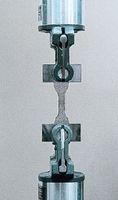
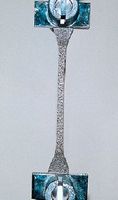
Adhesion
type of substrate | condition | adhesion N/mm2 |
---|---|---|
Concrete (standard pavement concrete) |
Cured for 28 days | 2.15 |
Damp concrete | Cured for 28 days | 1.60 |
Mortar | Cured for 28 days | 2.20 |
Coating mortar (mortar mixed with resin) |
Cured for 28 days (cured for 26 days after using mortar) |
1.10 |
Method
All waterproof layers examined in this test were subject to the B-1 method. Each material was pulled in a vertical direction after being set up in square steel jigs (4 x 4 cm) in the test.
All waterproof layers examined in this test were subject to the B-1 method. Each material was pulled in a vertical direction after being set up in square steel jigs (4 x 4 cm) in the test.
Chemical-Resistance
solution | status |
---|---|
Saturated concrete liquid | Normal |
Involving 2% of sodium hydroxide | Normal |
Involving 0.01% of hydrochloric acid | Normal |
Involving 20% of calcium chloride | Normal |
Sodium hypochlorite(20ppm) | Normal |
Seawater | Normal |
Machine oil | Normal |
Method
All the materials were soaked into each solution for six months after being set up on the slate plate by the B-1 method, and any swelling, cracks, peeling, and holes were subsequently examined.
All the materials were soaked into each solution for six months after being set up on the slate plate by the B-1 method, and any swelling, cracks, peeling, and holes were subsequently examined.
Impact-Resistance
system | condition | Fall height | |
---|---|---|---|
50cm | 100cm | ||
A-1 | Cured for 28 days | No cracks or peeling were found on any material. | |
B-1 |
Method
In accordance with JIS A6916, a 1 kg-steel ball was vertically dropped on the surface of each material from 50 cm and 100 cm height, and subsequently any cracks and peeling in the waterproof film were observed.
In accordance with JIS A6916, a 1 kg-steel ball was vertically dropped on the surface of each material from 50 cm and 100 cm height, and subsequently any cracks and peeling in the waterproof film were observed.
Pressurized Permeability
system | The permeability of each material was visually observed |
---|---|
A-1 | No permeability |
B-1 | No permeability |
No processing | Water penetrated and leaked after pressurized for 5 minutes. |
Method
In accordance with JIS A1404, 491 kPa water pressure was put on the material for one hour and any water leak was observed.
In accordance with JIS A1404, 491 kPa water pressure was put on the material for one hour and any water leak was observed.